
Classification and Application of YRT Turntable Bearings
YRT turntable bearings were initially mainly used in CNC turntables. However, during their usage, it was gradually discovered that YRT turntable bearings perform exceptionally well in equipment requiring high precision, such as medical instruments, precision rotary tables, and testing instruments.
YRT turntable bearings have become an indispensable part of the family of high-precision bearings.
Now, let me introduce the classification and applications of YRT turntable bearings.
- YRT Standard Turntable Bearings
The YRT standard turntable bearing features an outer ring rotation and inner ring support, forming a rotating motion structure. It consists of a thrust axis ring, a thrust washer ring, two roller retainer components, and a set of cylindrical rollers. There are evenly distributed screw mounting holes on the seat ring and axis ring, allowing direct fixation of the bearing with bolts. Preload is applied at the factory, eliminating the need for adjustment during installation.
YRT standard bearings are suitable for equipment with relatively short cycles, low friction, but higher requirements for bearing rigidity and precision. For example, they are used in rotating tables of machining centers, articulation rotation parts of industrial robots, rotary and precision rotary worktables.
- YRTS High-Speed Turntable Bearings
The external structure of YRTS high-speed turntable bearings is similar to that of YRT standard bearings, but there are significant internal differences. The YRTS series bearings have higher rotational speeds and lower and more uniform friction torque compared to YRT standard bearings. Therefore, they are suitable for equipment requiring low friction but higher rotational speeds, such as those driven by direct drive motors.
- YRTM Combination Bearings
Based on the YRT bearing, the YRTM combination bearing adds a bidirectional thrust cylindrical roller assembly for angle measurement systems. In other words, an angle measurement system is installed on the YRT standard bearing to more accurately measure and adjust the bearing's rotational angle, suitable for the higher precision operation of machinery. The measurement system consists of sensor components and measuring scales. It employs a pure inductive measurement principle, providing precise signals, making it one of the most accurate in this series of bearings.
This measurement system is rarely affected by external interference during operation, such as dust, oil stains, scratches, magnetic fields, etc., and does not require special maintenance.
It is generally used in fields where high rotational precision in terms of angles is required, such as indexing heads, military radar, high-precision rotary worktables and shafts, aerospace-grade measurement and testing devices.
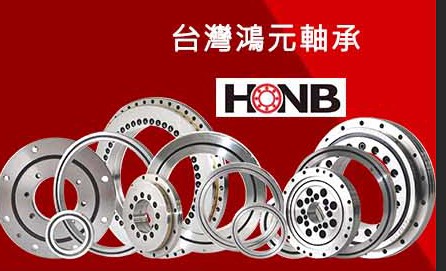